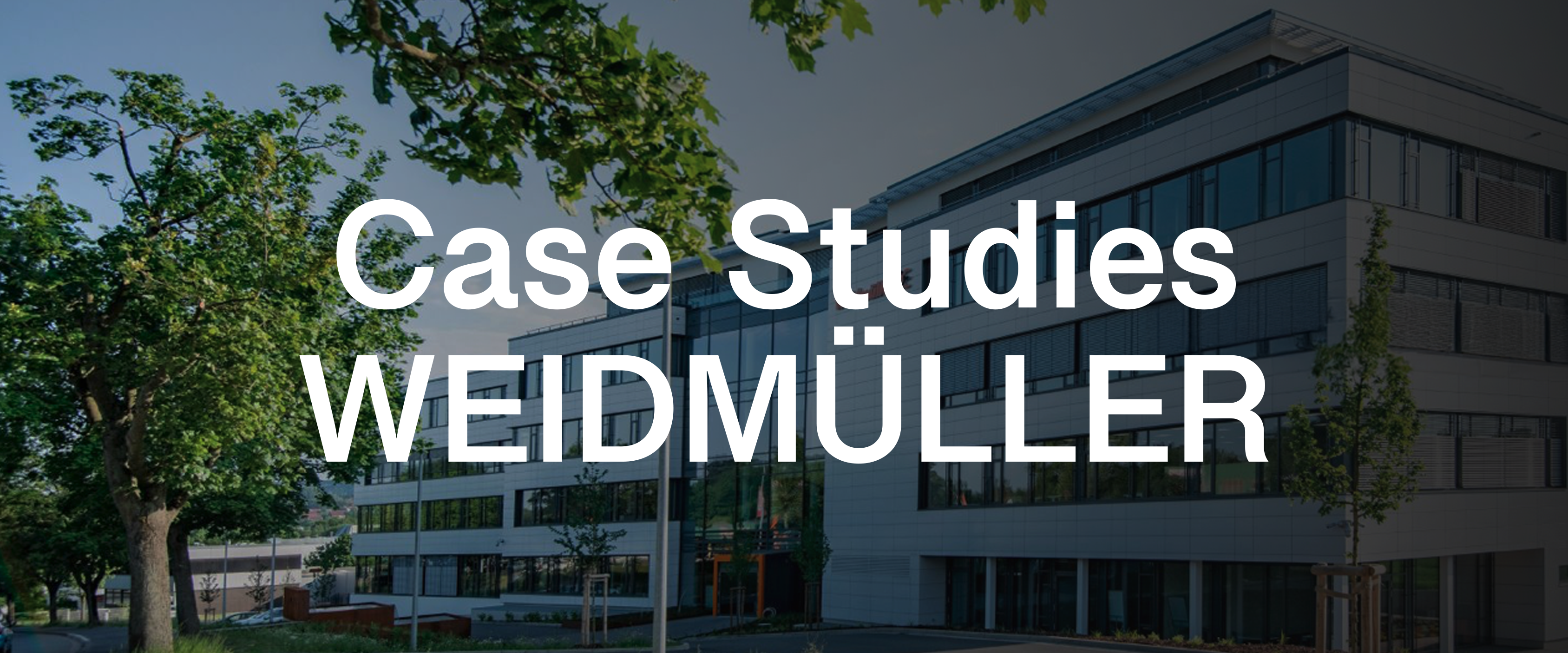
Weidmüller Enhances Production with
Reliable and Faster Deliveries

INDUSTRY
Electrical Connection Technology
CHALLENGE
Lack of transparency in production processes affecting delivery reliability
IMPLEMENTATION TIME
2.5 months (From Kick-off to Go-Live)
RESULTS
↑ 30% More On-Time Deliveries
↓ 20% Less Lead Times
THE MANUFACTURER
Weidmüller is a global leader in industrial connectivity solutions, specialising in power, signal, and data applications. Thüringische Weidmüller GmbH, established in 1990 in Wutha-Farnroda, Germany, is one of the key manufacturing sites of the Weidmüller Group.
At this location, over 300 employees focus on manufacturing components primarily for printed circuit board connection technology.
The site is also equipped with state-of-the-art production systems. In recognition of its outstanding quality standards, the site was awarded the Thuringian State Award for Quality in 2010.
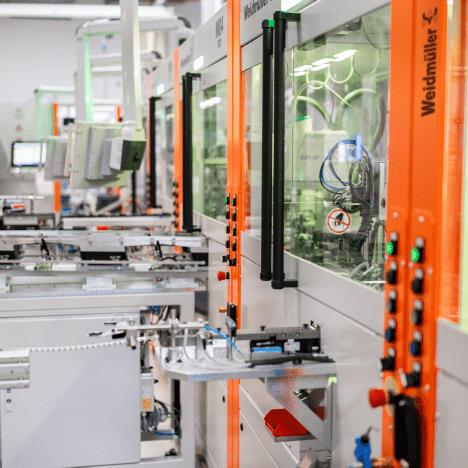
THE CHALLENGE
Lack of Visibility into Production Orders
Thüringische Weidmüller GmbH faced difficulties in tracking the status of production orders in real time. This lack of visibility made it difficult to align priorities effectively, often leading to delays and missteps in the production process.
Inefficient Task Prioritisation
The absence of a structured system for prioritising tasks added to the complexity of managing production. Critical jobs were often delayed because there was no reliable way to identify and focus on the most important tasks, especially during unexpected changes in production schedules.
Resource Allocation
Scheduling workers efficiently and managing the availability of manufactured parts posed additional challenges. Without a clear system to indicate when components were ready for reuse, delays and inefficiencies became common, impacting overall production flow and operational efficiency.
Impact on Delivery Reliability
These issues collectively affected the company’s ability to meet delivery commitments consistently. Delays, inefficiencies, and a lack of transparency in production processes highlighted the need for a robust planning solution to enhance operational control and improve delivery reliability.
THE SOLUTION
Thüringische Weidmüller GmbH implemented the planeus planning system to enhance process visibility and streamline production. Key features and outcomes included:
Comprehensive Order Tracking and Management
planeus offers a flexible order management structure for manufacturers to create and manage production orders in a quick and easy.
• Real-Time Visibility: planeus provides a clear and up-to-date view of every production order’s status, ensuring all stakeholders can access the latest information instantly.
• Project-Based Order Management: Users can create production orders within projects, each containing one or multiple articles (order items). This scalable setup accommodates both simple and complex production runs.
• Bulk Editing and Updates: This feature allows users to edit and update multiple production orders simultaneously, streamlining adjustments across various items efficiently.
• Advanced Sorting and Filtering: Orders can be sorted and filtered by key parameters such as status, delivery date, location, or customer, enabling precise order tracking and prioritisation.
Optimised Resource Utilisation
• Integrated Gantt Chart and Dashboard: Resource usage and capacity are displayed on Gantt charts and dashboards, making it simple to monitor and manage upcoming resource allocations in real time.
• Future Capacity Planning: The system provides a detailed breakdown of utilisation levels by day, week, month, or a full year in advance. This enables planners to anticipate workloads, identify potential resource shortages, and allocate resources effectively across future timeframes.
• Proactive Adjustments: With immediate visibility into projected workloads, planners can quickly detect over-committed resources and adjust schedules to optimise capacity and prevent delays.
Transparent Workforce Management
• Qualification Matrix: planeus incorporates a qualification matrix, linking specialists with their qualifications, ensuring important tasks will be performed by their qualified staff.
• Indication of Work Shift Impact: planeus incorporates worker shifts into production schedules, ensuring smooth coordination between shifts and allowing for dynamic shift adjustments that will have positive impact in productivity.
• Indication of Maintenance Impact: Maintenance activities are displayed as capacity gaps. When deivations happen, affected tasks will be adjusted and prolonged, ensuring transparency and operational continuity.
THE RESULTS
planeus delivered significant improvements for Thüringische Weidmüller GmbH, including:
• On-Time delivery rate increased by 30%
• 20% reduction in production time
• Digital transformation in just 2.5 months
• Increased transparency and control
LOOKING AHEAD
Weidmüller is committed to maintaining the gains achieved through the implementation of planeus. By leveraging the follow-up support and Potential Check of planeus, the company continues to fine-tune its processes, improve machine utilisation rates, and enhance overall efficiency. The collaboration with planeus ensures that Weidmüller remains agile and well-equipped to adapt to future challenges, sustaining their operational excellence and commitment to delivering high-quality products on time.